Sustainability
We act today, because we think about tomorrow.
While crafting products of enduring beauty and utility, in the heart of every great company lies a promise to Mother Earth.
Our Philosophy
From the moment raw materials are sourced to the firing of our creations, every process is filled with reverence for the planet.
We implemented transformative processes that stand as a testament to our vision and we’re always looking for new measures that allow decarbonization and increase energy efficiency.
In our pursuit of a more harmonious relationship with our planet, we’ve embarked on an inspiring journey of sustainability.
We’ve delved deeper, integrating ingenious heat recovery systems and innovative water treatment processes.
Every droplet utilized in our production is cherished, treated, and lovingly reused, reflecting our dedication to responsible stewardship.
Looking ahead, the horizon brims with promises of further sustainability endeavors.
We envision harnessing the warmth from our air compressors, electrifying our firing process, and gracefully transitioning to renewable energy sources for drying.
Together, we’re not merely building a future, we’re crafting an opulent tapestry of sustainability, weaving threads of hope and vitality.
Our Jorney
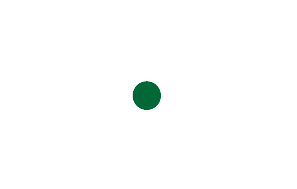
2018
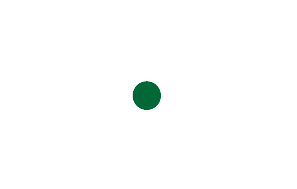
2018
3 million pieces capacity installed
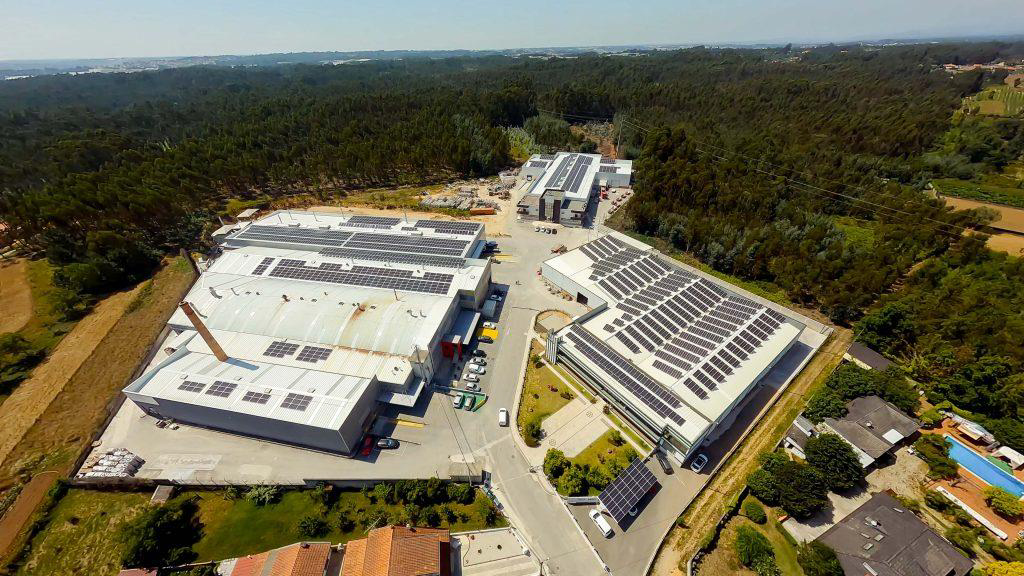
2019
1st solar plant installed
25% self sufficient
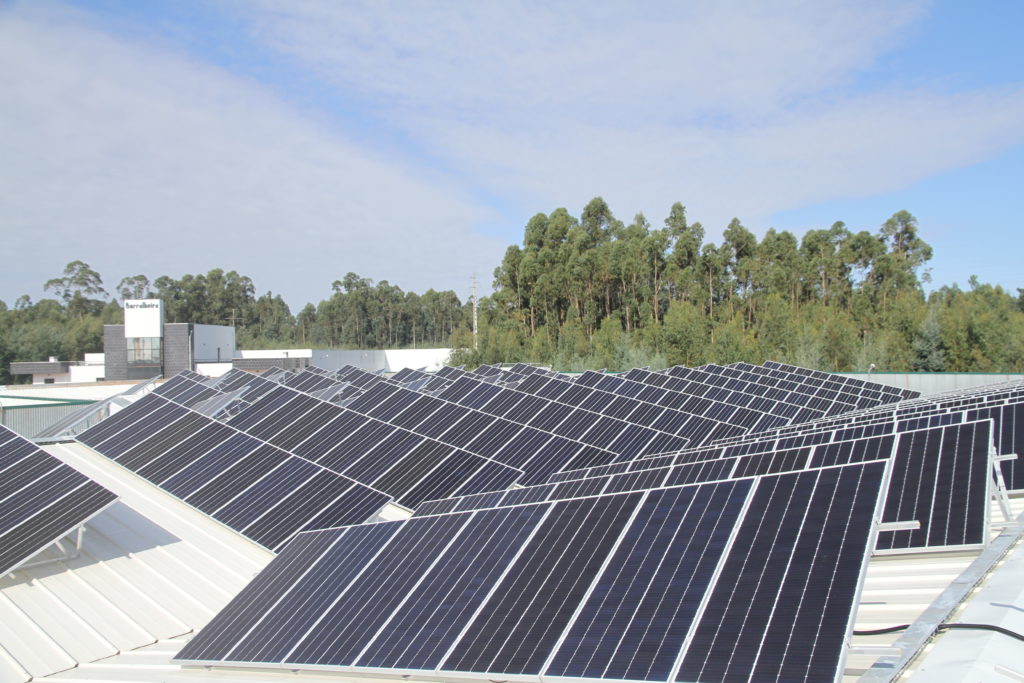
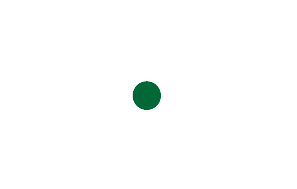
2019
2020
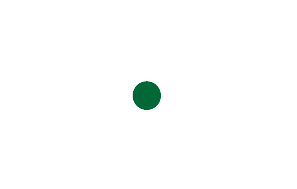
2020
2nd solar plant installed
35% self sufficient
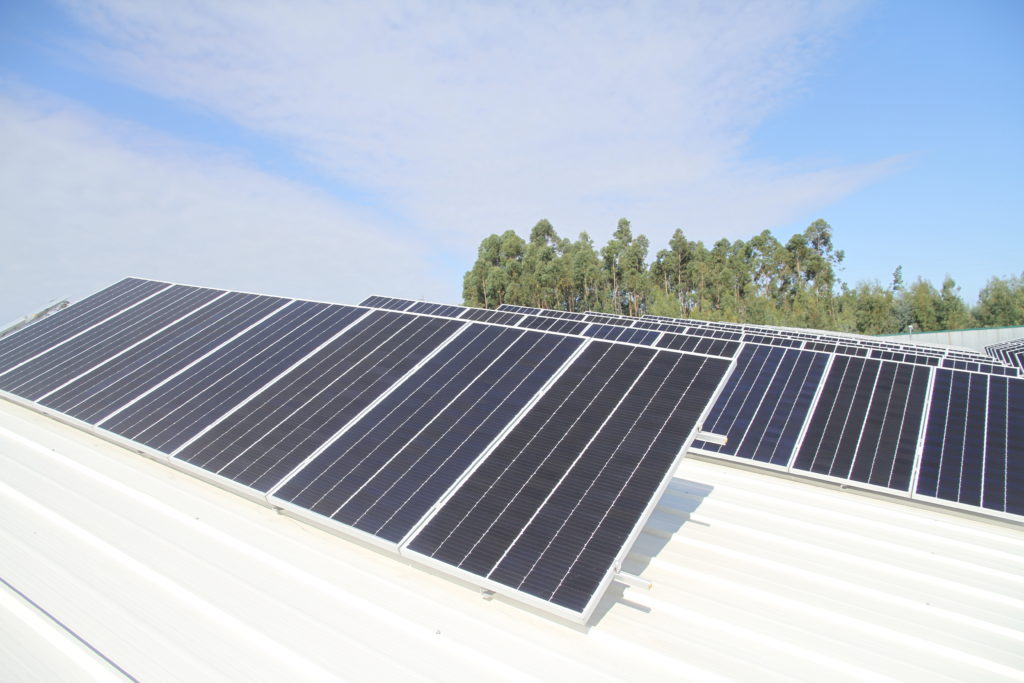
New building construction
+3300 sqm
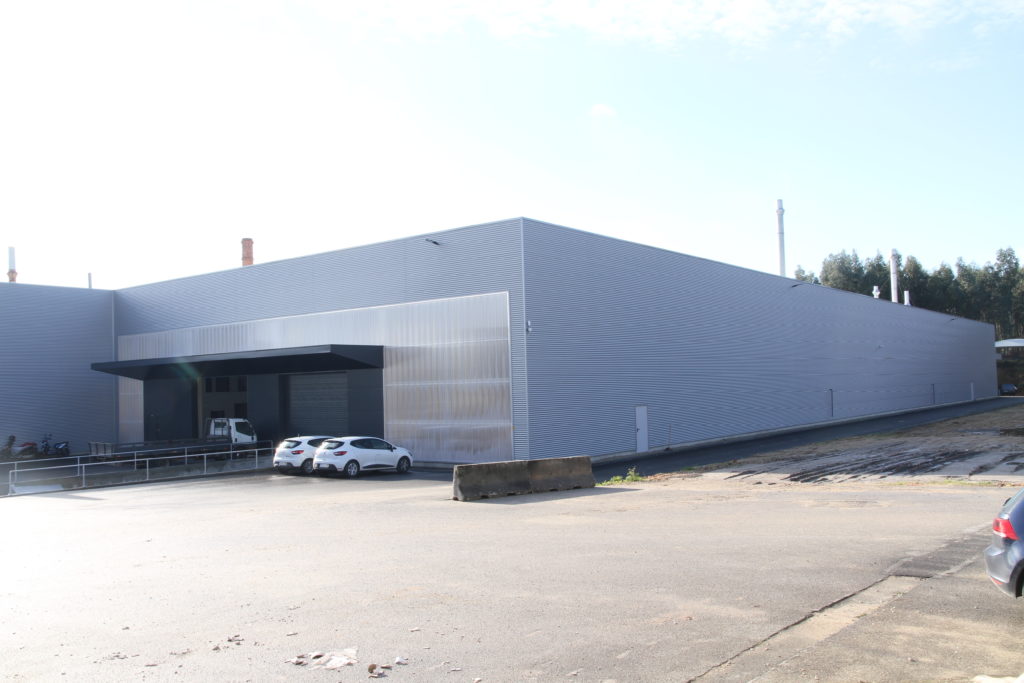
Rain water harvest system
300 000L
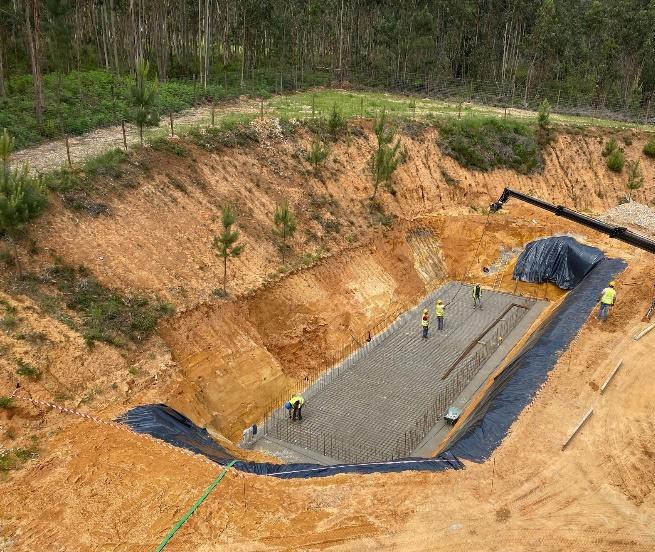
Self sufficient for 18 days without rain
2021
3rd solar plant installed
40% self sufficient
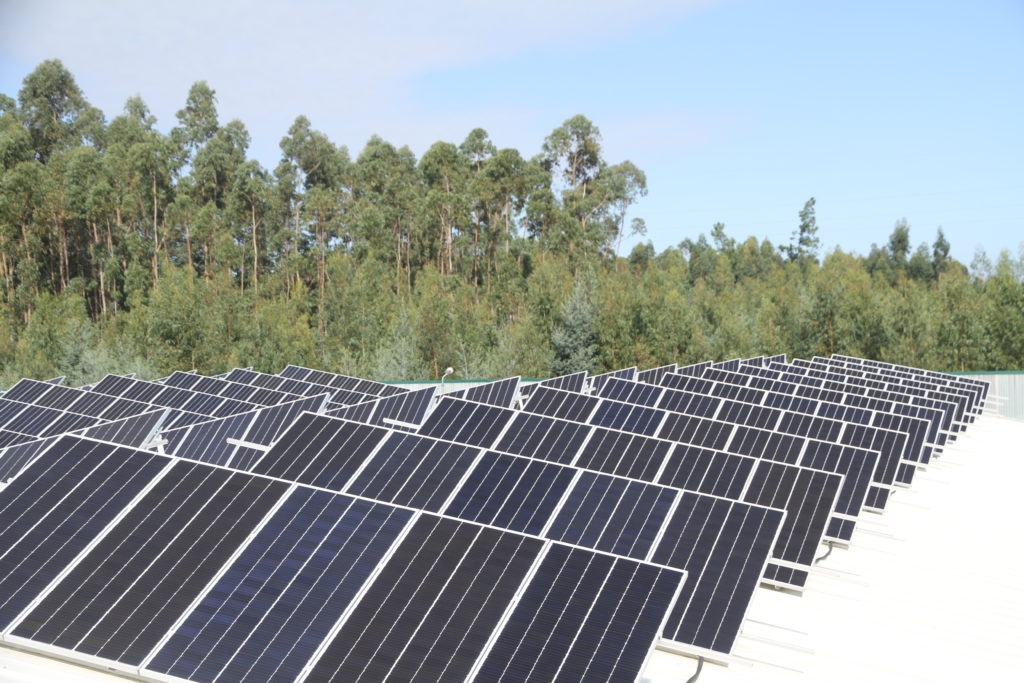
New roller kiln
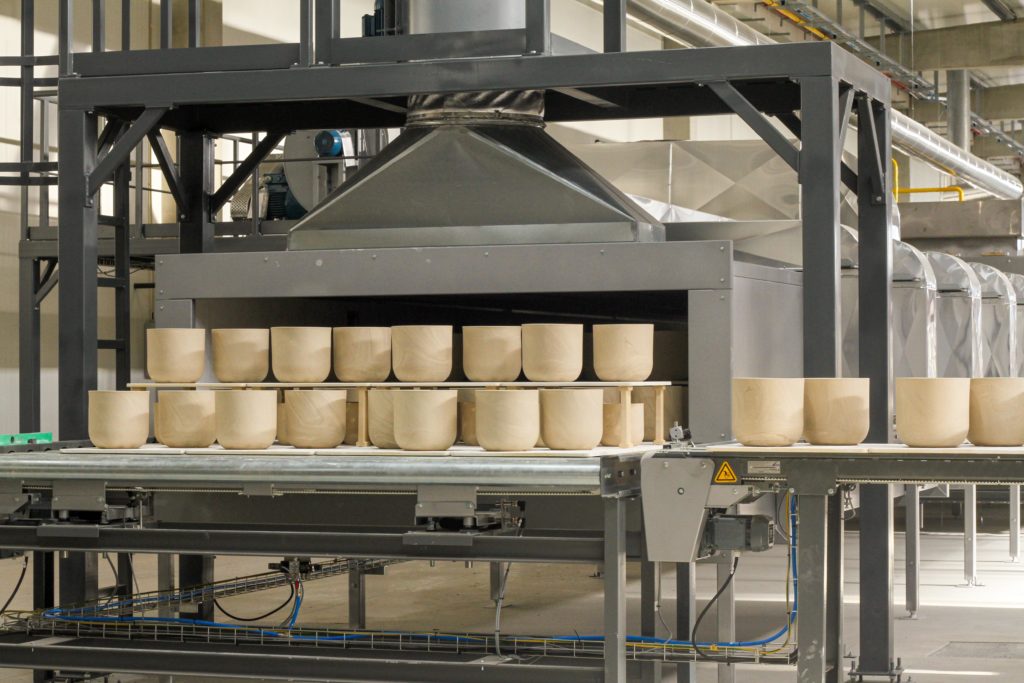
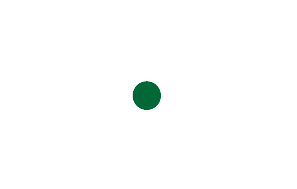
2021
2 new LEAN production lines
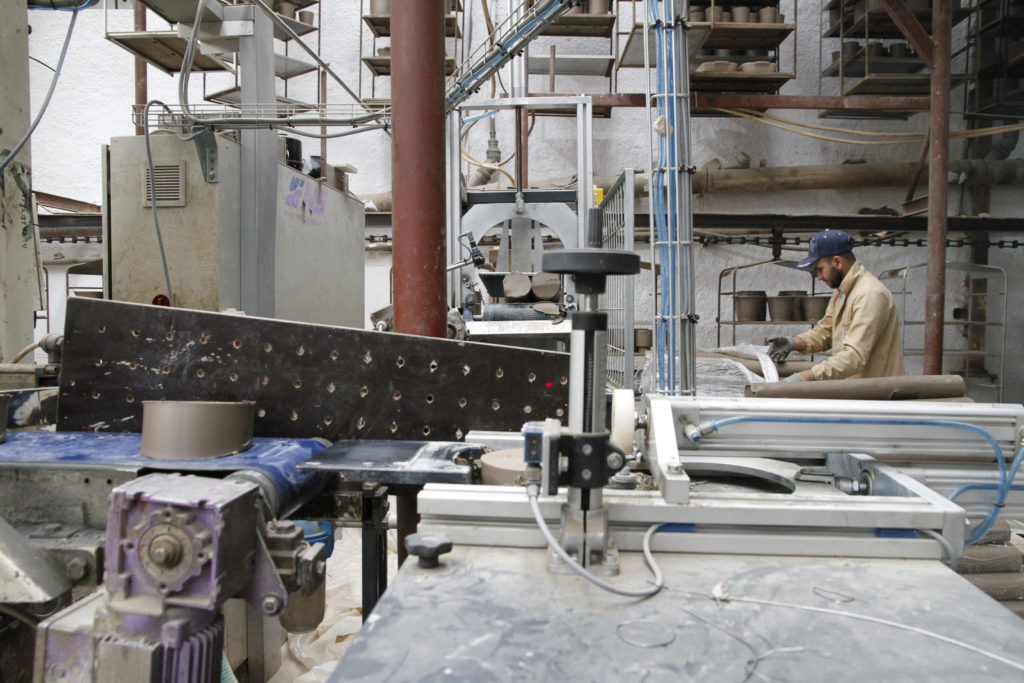
1st automatic packaging line
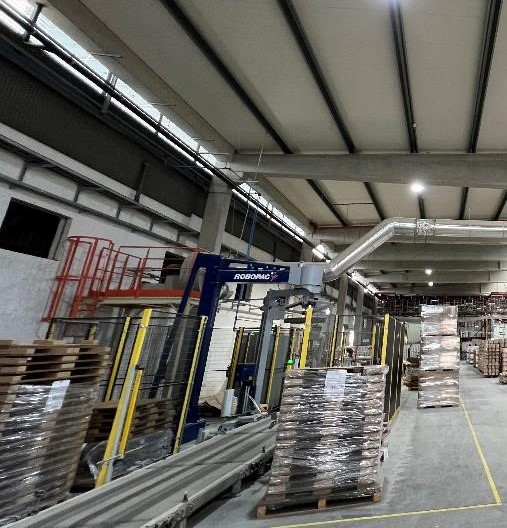
2022
Heat recovery system
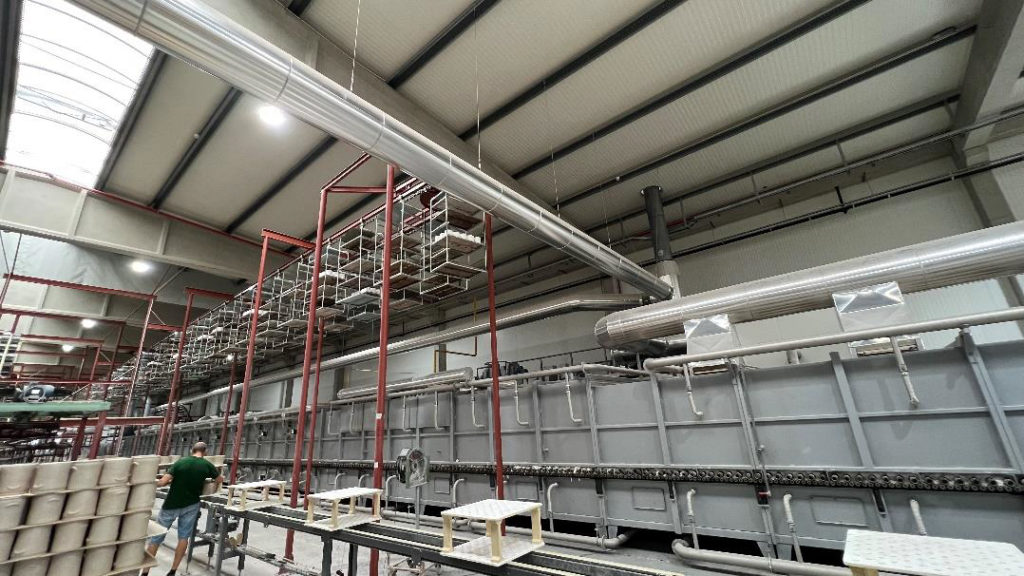
From the kiln to the dryer
2nd & 3rd automatic packaging lines
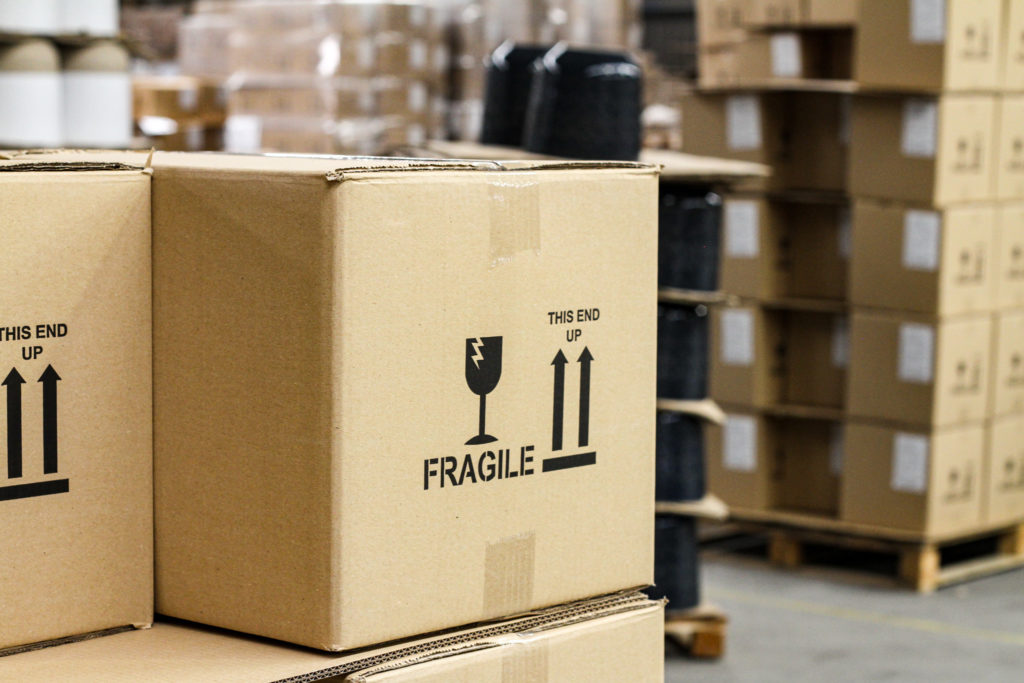
Air conveyor expansion
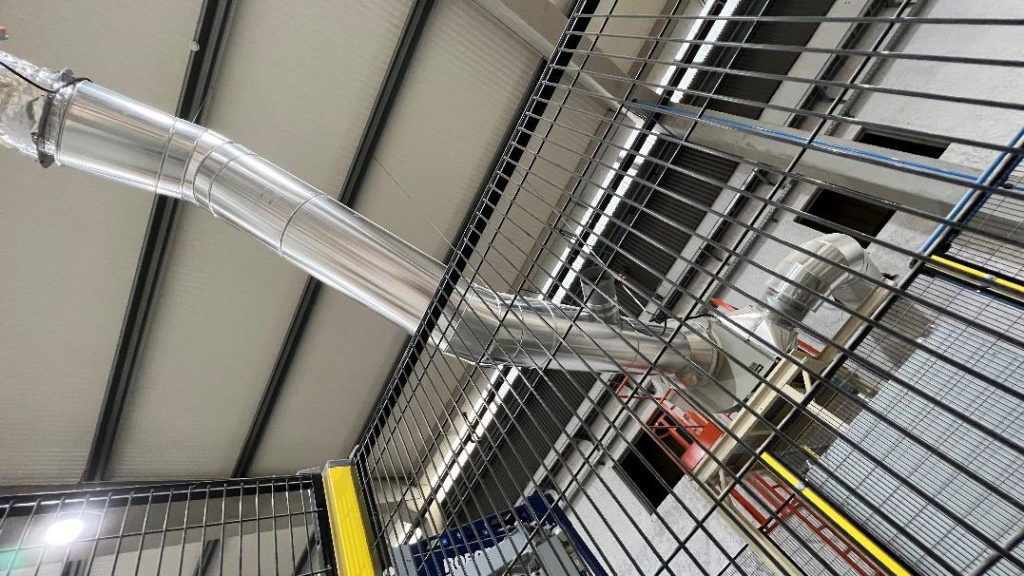
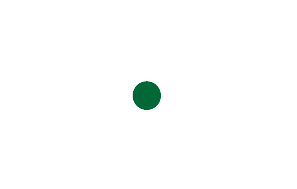
4th solar plant installed
50% self sufficient
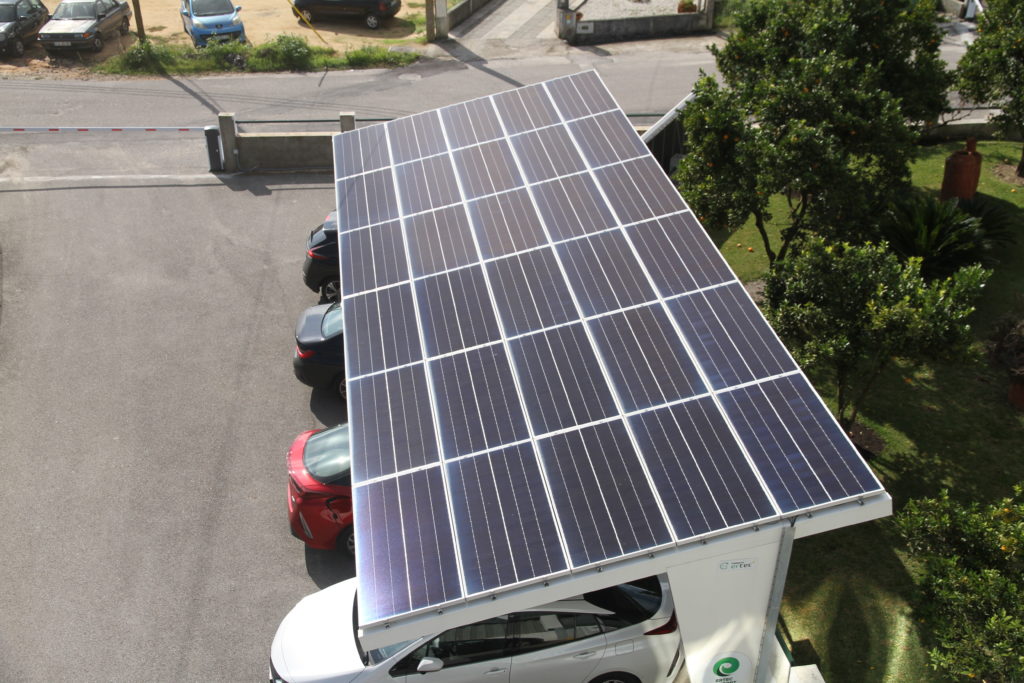
3 new LEAN production lines
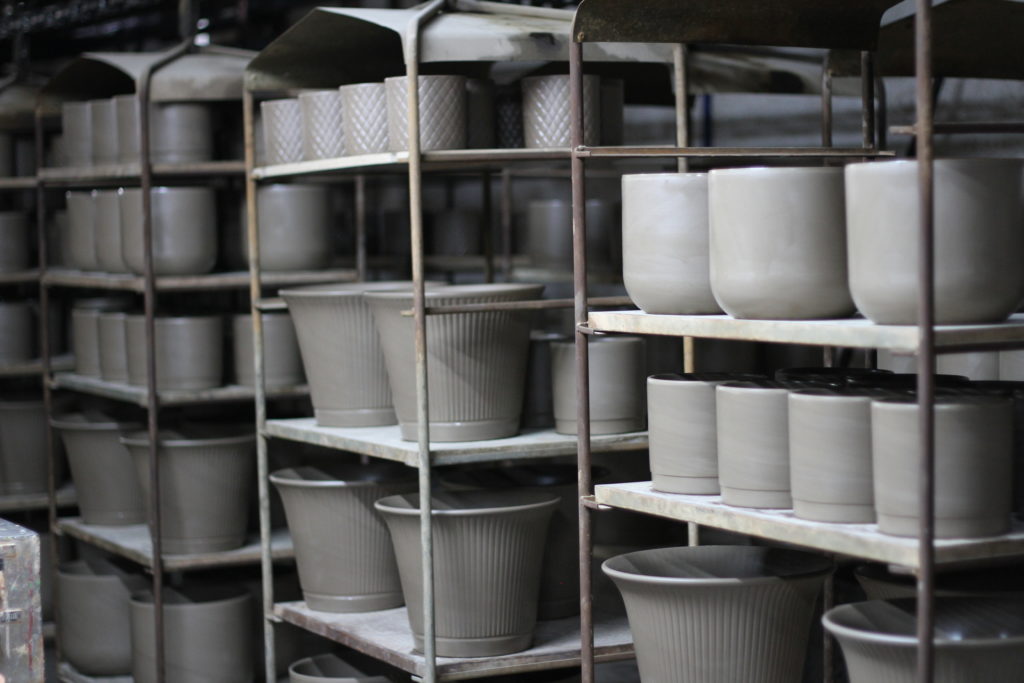
1st vacuum system
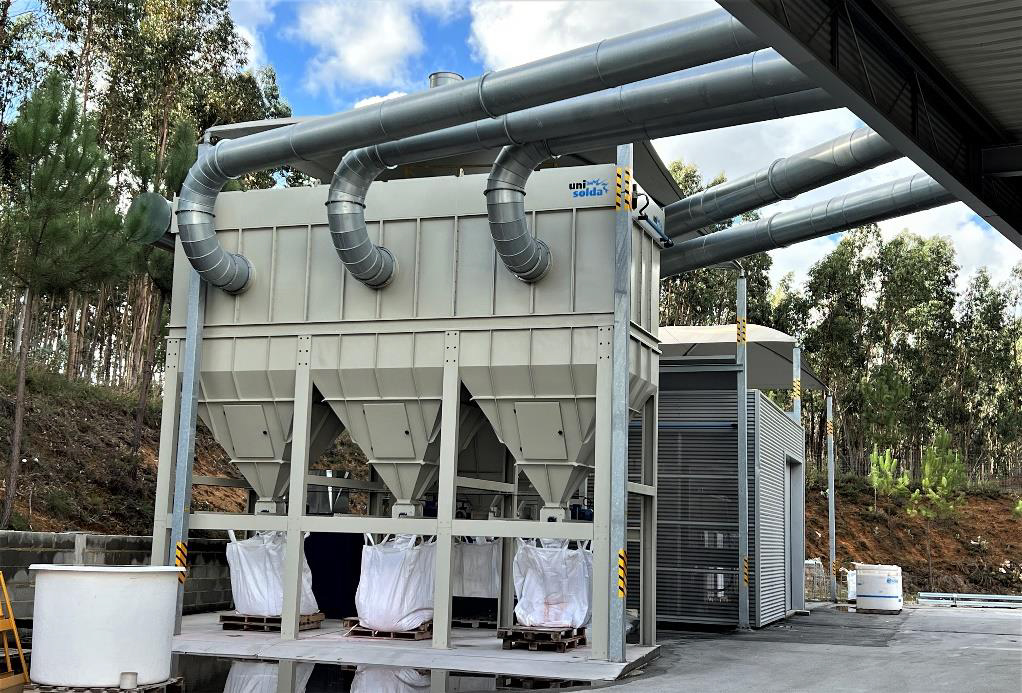
The system avoids releasing particles into the air.
Instead, they are collected into big bags and reused in the glazing process again.
2023
Clay production expansion 100 tons per day 4 different colors
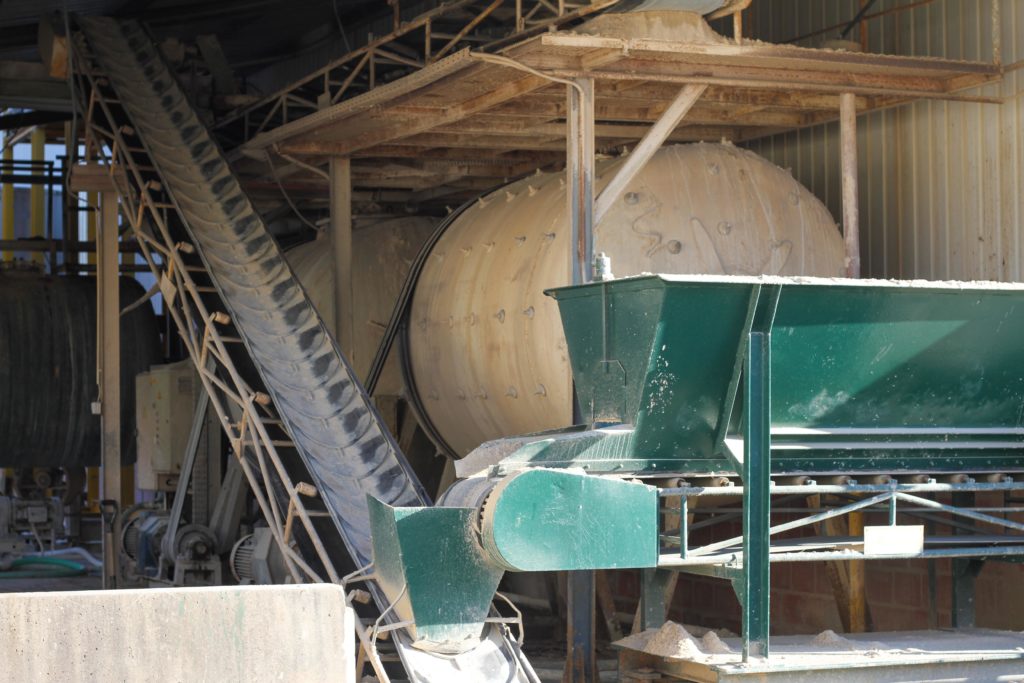
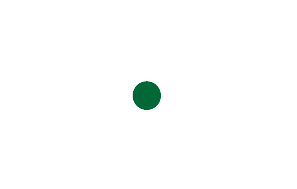
2023
2024
In progress
Automatic polishing line
New water treatment station
Unit to process fired scrap pieces
5th solar plant 65% self sufficient
2 new glazing machines
2nd vacuum system
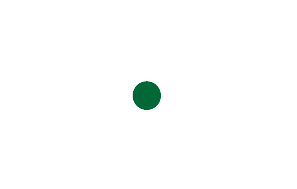
12 million pieces capacity installed
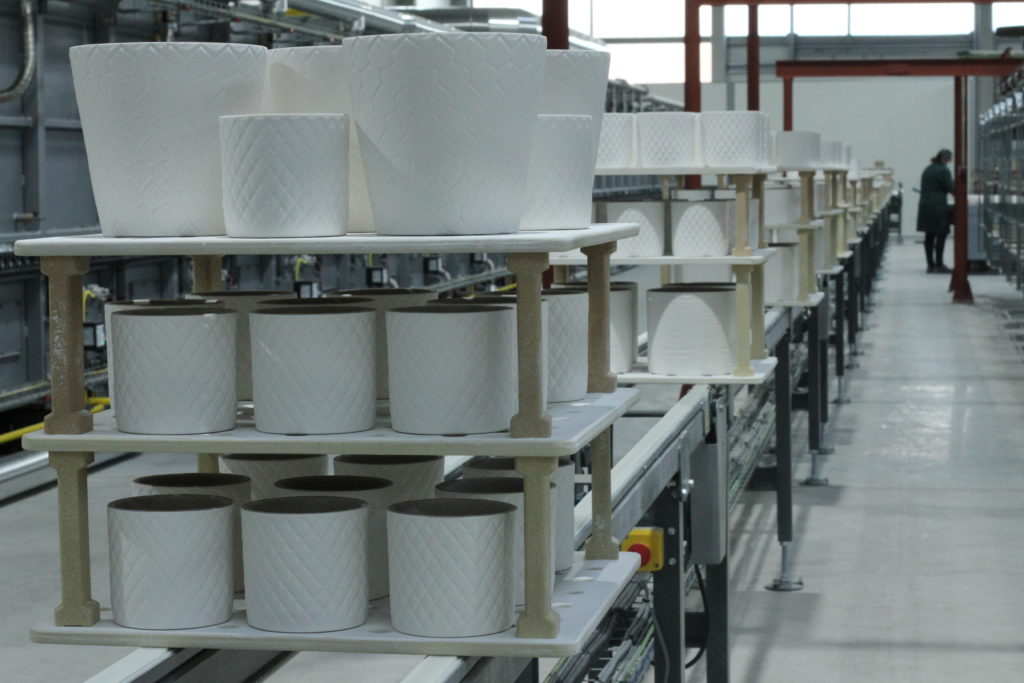
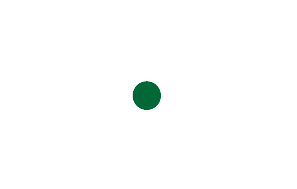
Upcoming Exploration
2025
Heat pump system + storage battery
EMS – Energy Management System
Automatic slip casting
Automation on extruders
2026
6th solar plant (80% self sufficient)
Construction of a new building (+4500 sqm)
2027
Automatic storage warehouse
Hydrogen production (in order to replace up to 50% of natural gas used)
Daily measures
Water treatment
All water used in our production is treated in our premises and reused afterwards.
Raw material savings
Vacuum pug mill implanted
(approximately 3.5Kg of reused clay per day).
The dry clay and shavings that come out of the machines, which do not yet have a vaccum pug mill are reintroduced into the production process.
Glaze reuse
In our new production unit glazing machines have a suction system that allows the glaze to be reused.
The vaccum system collect the glaze, dry it and transform it into powder, which is later reinserted into the production process.
Natural light
Creating a better working environment and reducing electricity consumption.
Waste separation
We separate the waste produced in our factory and send it to a team for treatment.
Water treatment
All water used in our production is treated in our premises and reused afterwards.
Raw material savings
9 vacuum pug mill implanted
(approximately 9000Kg of reused clay per day).
The dry clay and shavings that come out of the machines, which do not yet have a vaccum pug mill are reintroduced into the production process.
Glaze reuse
In our new production unit glazing machines have a suction system that allows the glaze to be reused.
The vaccum system collect the glaze, dry it and transform it into powder, which is later reinserted into the production process.